製缶板金・組立溶接加工
板金加工について
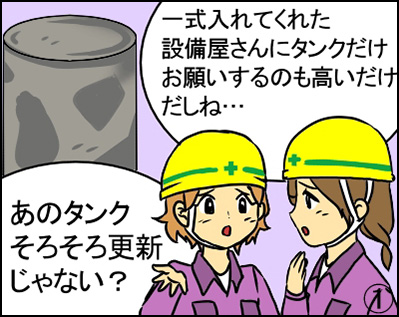
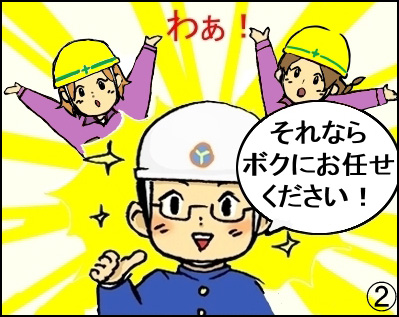
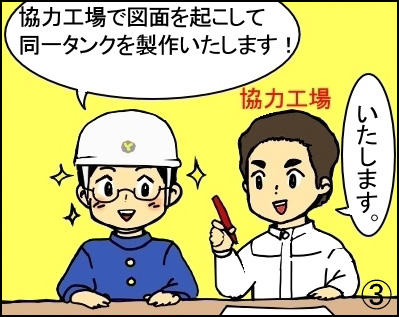
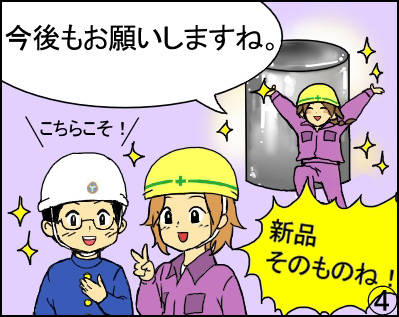
板金加工は、けがきから始まります。けがきとは、薄板の素材に板金加工する形状の展開図を書き込むことをいいます。この作業は、けがき針でひっかくことからけがき作業とよばれます。けがき作業の後、けがきを入れた板金から必要な形状の素材を切り出します。一方、けがきを入れた板金を、折り曲げる場合もあります。これを板金折り曲げといいます。さらに、平板を円筒形に丸める板金もあり、これを板金曲げといいます。ここまでが板金加工の準備段階です。切り出した板金は、工具で叩いて成形します。この叩き出しは、板金加工の中で最も神経を使う作業です。平板を立体的な形状にする過程では、薄くなったり、それが重なったりします。これを無理のないように叩き広げていくためには、加工している対象をよく観察しながら行う必要があります。変形が大きな板金加工の場合は、絞り出しをします。円筒形に成形したり、叩き出しや絞り出しで加工した部品は、組み合わせて一体化する必要があります。この作業が接合です。接合方法としては、溶接やはぜ組みがよく用いられます。
①.板金の切断
板金を手作業で切断するためには、工具・電動工具・機械を用います。この他、ダイとパンチを用いて、穴をあけたり打ち抜いたりするプレス加工を行うケースもあります。
Ⅰ.板金切断用工具
板金切断用工具には、金切りばさみ・金切りのこ・たがね・押し切りがあります。
- 金切りばさみ
金切りばさみは、はさみで紙を切るのと同じ要領で切断します。直線を切断するには刃が真っ直ぐな直刃、曲線を切断するには刃が曲がっている柳刃やえぐり刃のはさみを使用します。 - 金切りのこ
金切りのこは、のこぎりで木材を切断する要領で板金を切断します。万力などに板金を固定して、のこ刃を板金に直角に当てて切断します。 - たがね
たがねは、ハンマーと組み合わせて使います。鋭く研いだタガネの刃先をハンマーで板金に打ち込んで、板金を切断します。 - 押し切り
押し切りは、直線状の切断を行うために用います。レバーになったシャーを押し下げて、シャーの間に挟んだ板金をせん断により切断します。
Ⅱ.板金切断用電動工具
板金切断用電動工具には、ハンドシャー・ニブラ・ジグソーがあります。人力をほとんど使用せずに板金を容易に高速で切断できるため、板金加工では重宝されています。
- ハンドシャー
ハンドシャーは上刃と下刃の間に板金を挟む方法です。上下に往復運動する上刃と固定された下刃の間に板金を入れ込んで次々と切断していきます。 - ニブラ
ニブラはポンチを高速で上下に動かして、ダイとの間に挟んで切断する方法です。 - ジグソー
ジグソーはのこ刃を電動で往復運動させて切断します。取扱いが簡単なため、日曜大工などでも多く使われています。 - プラズマ切断機
プラズマ切断機はこれらの機械的な電動工具とは切断方式が異なり、高温プラズマで板金を溶断するものです。取扱いが簡単で効率が良いので現場でよく使われています。
Ⅲ.切断用の専用機械
切断用の専用機械は、他の切断方法と異なり、コイルなど長尺の金属素材を切断するときに用います。専用機械には、スケアシャー・ロータリーシャー・スリッターなどがあります。これらは、工具の間に板金を挟んで、連続して直線状に長く切断できるといった特徴があります。この他に、プレス加工機での切断があります。ダイとパンチで切断できる長さはプレス加工機の大きさで決まります。ブランク板と呼ばれるような、決められたサイズの板の加工に適しています。
②.板金の曲げ加工
板金の曲げ加工には、線状に曲げる折り曲げ、円筒状に曲げる丸曲げ、および円板や円筒の縁を曲げる縁曲げがあります。いずれの曲げ加工も、板金の下に置く台と、叩く工具の組み合わせで行います。
Ⅰ.板金の折り曲げ加工
板金の折り曲げ加工は、けがき線に沿って直線状に長く曲げる加工です。工具は、折り台と拍子木を用いる方法と、刀刃と拍子木を用いる方法があります。折り台とは、鋼板をはりつけた木材です。この端にけがき線を合わせて、樫の木でできた拍子木で、けがき線の近傍を叩いて折り曲げます。折り台や刀刃の他に、影たがねとよばれる工具と拍子木を用いる場合もあります。
Ⅱ.板金の丸曲げ加工
丸曲げ加工は、板金を円筒形に曲げる加工方法です。台とパイプを用いて、板金をパイプの曲面に沿って、拍子木と手で曲げていきます。曲げ加工で円筒を作る場合は、拍子木で叩いて鼻曲げ加工を行います。
Ⅲ.板金の縁曲げ加工
縁曲げ加工は、円板や円筒の縁を曲げる加工方法です。工具を用いて打ち出し、もしくは絞りによって成形する方法です。円板の縁曲げ加工は、円板の縁をならしと呼ぶ台において、木製のハンマーで叩きながら、少しずつ回転させて縁を打ち出します。加工中、縁には絞られるためにしわが寄りますが、このしわを重ねてしまうと割れてしまいます。できるだけ重ならないように作業を繰り返すことがポイントとなります。
③.板金の打ち出し加工と絞り加工
板金の打ち出し加工と絞り加工の違いは、その加工方法です。両者はどちらも同様の立体的な形状を作り出しますが、加工する場所が大きく異なります。打ちだし加工は、板金の中央部から縁にかけてハンマーで叩いて伸ばしていきます。板金を叩いて、次第に深いくぼみを作る要領です。一方、絞り加工は、成形する板金の縁を少しずつ叩いて絞っていきます。周辺部をぐるぐる廻しながらの加工になります。
④.板金のひずみ取りの加工方法
Ⅰ.平面板金のひずみ取りの加工方法
板金加工をしている最中は、平面部に様々なひずみが発生します。平板の中央でひずみが生じたときは、板がふくらみを持ちます。こうした平板の真ん中で生じたひずみを取るためにはつち打ち法を用います。つち打ち法で重要になるのが、ひずみでふくらんだ部分を直接叩いてはいけないということです。不用意に叩くと、逆にひずみが大きくなる可能性があります。つち打ち法でひずみを取るためには、ふくらみの周囲を叩いてひずみを周囲に散らばらせることが大切です。
Ⅱ.曲面のひずみ取りの加工方法
板金の曲面のひずみ取りは、まず、ひずみで膨らんでいる方向を裏面にし、ふくらみを曲率が小さな当て盤(ドリー)にのせ、周囲をハンマーで叩きます。これをオフドリー作業といいます。その後、平らな当て盤にのせ、凸部をハンマーで叩き、できるだけ平滑な面にします。これをオンドリー作業といいます。最後に、平らな当て盤の上に加工品をのせ、仕上げハンマーでならし作業を行い、平滑な面に仕上げます。これをオンドリーならし作業といいます。
Ⅲ.灸すえ絞り法
実際の金属加工で、最も簡便且つ迅速にひずみを取り去る方法が灸すえ絞り法です。やり方は、ひずんでふくらみがある部分をアセチレンガスバーナーなどで約700℃まで加熱し、その後、水や水を含ませたスポンジなどで急速に冷やします。こうすることで、ふくらんでいた部分に引張応力が働きひずみが無くなります。
⑤.板金の接合
接合には、機械的接合法と冶金的接合法があります。機械的接合の主なものとして、はぜ組み・リベット・ボルト締めがあります。冶金的接合の主なものは溶接です。
Ⅰ.はぜ組み
はぜ組みは、板金の端を折り曲げて組み合わせる接合方法です。板金加工だけではなく、薄鋼板の接合にもよく使われます。缶詰の銅の部分に縦線が入っていますが、これがはぜ組みです。
Ⅱ.リベット接合
リベット接合とは、リベットを用いて板金や形鋼を接合する方法です。板に穴をあけておき、リベットを差し込み、片方を変形させて接合します。リベットは溶接法の進歩で使われなくなりつつあります。また、ボルト接合に取って替わられる場合も多いです。
Ⅲ.溶接
溶接については以下で詳しく触れます。
溶接について
溶接とは、2枚の金属板を向い合せで並べ、この向かい合った場所を加熱して溶かし、液状になった金属組織を混ぜ合わせた後に冷却して固め、バラバラであった2枚の板を1枚の板のようにしたり、局部的に大きな電流を通すことで抵抗発熱を生じさせて板の接触部を半ば溶けるまで加熱し、さらに圧力を加えて強固に貼り合わせるなどの方法や技術のことを指します。ボルトやナットや接着剤を使用した接合法よりも強度があり、ボルトやナットを使わないため製品自体も軽くなり、作業効率も高いことからあらゆる分野に溶接は使用されています。
①.溶接の長所と短所
溶接は、材料をつなぐ方法として強度が高く、簡単である反面、極めて高温で作業を行わなければならないので十分な注意が必要です。
Ⅰ.溶接の長所
溶接の長所は、接合部分の強度が高いため、大型の構造物を製作することができる点や、ボルトやナットを使用する場合と異なり、板に穴をあける必要がないので作業工程数が削減され、工期が短くなるといった点です。また、ボルトやナットや当て板を使用しなくて済む分、製品の重量を減らすこともできます。その他の長所として、つながれた部分が互いに溶け合っているので液体や気体が漏れない点や、単純な溶接の反復作業や変化のない長い溶接線の溶接作業などは人手を省いてロボットや自動溶接装置にさせることができる点などがあげられます。当然ながら、リベット止め作業などに比べて騒音の発生が少ない点も長所といえます。
Ⅱ.溶接の短所
溶接の短所は、急激に材料を加熱するので材料が変質しやすい点や溶接された場所が冷えると接合部分が縮んで板が変形することがあり、変化が起こらないよう板を無理に抑えつけて溶接すると、今度は板の内部にストレスがたまり、後で溶接部分が割れてしまう恐れがあることです。また、作業者のスキルに依存する割合が高く、良い溶接が行われているかどうかといった溶接内部の状態を調べることができないところも短所といえます。
②.主な溶接方法
Ⅰ.融接法
- 被覆アーク溶接
被覆アーク溶接は被覆アーク溶接棒と溶接される母材とを交流または直流のアーク溶接機に接続し、溶接棒の先端と母材との間にアークを発生させ、その高温により溶接棒と母材の接合したい部分とを溶かして混ぜ合わせることにより接合する方法です。 - マグ溶接
マグ溶接は、アーク溶接部の周囲をなんらかのガスで包み、大気中の酸素や窒素の悪影響を受けないように保護しながら行う溶接法の一種で、現在主流となっている半自動溶接の代表格といえます。 - ミグ溶接
ミグ溶接のミグとは、Metal Inert Gas weldingの頭文字をとった造語です。イナート(Inert)とは、他の物質と反応しない性質を意味しています。ミグ溶接は、マグ溶接と異なり母材が空気中の酸素等に酸化されないため、マグ溶接ではできないアルミニウムなどの酸化されやすい金属の溶接を行うことができます。 - ティグ溶接
ティグ溶接のティグとは、アルファベットのTIGを並べたものです。IとGについては、ミグ溶接と同じ意味を持ちます。Tはタングステンのことを表しています。つまりティグ溶接は、融点が非常に高く消耗しにくいタングステンを電極材料として使い、これと母材との間にアークを発生させ、その周囲をアルゴンやヘリウムなどの不活性ガスで包み、溶加材を補給しながら溶接を行います。 - プラズマ溶接
プラズマ溶接は、特殊なトーチの内部で発生させたアークに、アルゴンや窒素などのガスを送り込み、アークの高温で加熱され膨張した高熱のガスを、トーチ先端のノズルから高速度で噴出させて、これを溶接に利用する方法です。このとき、高速度で噴出する高温のガスをプラズマジェットといいます。 - レーザービーム溶接
レーザービーム溶接は、溶接の熱源としてレーザー光のエネルギーを利用するものです。レーザー光は指向性が良く、これをレンズで絞り、微細なスポットに集めたときのエネルギー密度が高いため、溶接、切断などの材料加工の分野をはじめ、医療分野、情報分野、計測分野など多くの分野で使用されています。
Ⅱ.圧接法
- スポット溶接
スポット溶接は、重ね抵抗溶接の代表としてあげられる溶接であり、薄板の高能率溶接に適した溶接法です。他の多くの溶接法と異なり、作業者の熟練を必要としないため自動化・ロボット化がしやすく、自動車メーカーや家電メーカーなど大量生産する現場で多く用いられています。 - 冷間圧接
冷間圧接は、主としてアルミニウムや銅、スズ、亜鉛など展性、延性に富む非鉄金属、もしくは鋼を、電気やガス、化学薬品などの熱源を一切用いずに、常温のもとで、機械的に圧力を加えるだけで接合させる方法です。 - 摩擦圧接
摩擦圧接は互いに端面同士を突き合わせた両母材に圧力を掛け、一方の母材のみを回転させたり、または両方の母材を逆方向に回転させたりして相対運動を与え、これによって生じた摩擦熱で接触面が適切な温度に達したときに両母材間の相対運動を止め、同時に圧力を増して圧接する方法です。