樹脂・特殊素材加工
樹脂・ゴム
樹木の脂(やに)を原料としたものを天然樹脂、石油を原料として合成的に作られたものを合成樹脂といい、プラスチックは合成樹脂の一種です。ゴムにも天然ゴムと合成ゴムがあります。
Ⅰ.樹脂
樹脂とは、元来は樹木の脂(やに)を原料とした粘性のある物質を指し、天然の素材からできたものを天然樹脂、石油を原料として合成的に作られたものを合成樹脂といいます。合成樹脂には、熱を加えると柔らかくなる熱可塑性樹脂と、熱を加えると硬くなる熱硬化性樹脂の二種類があります。熱可塑性樹脂の一種であるプラスチックは、可塑性が高く、様々な製品に利用されています。
Ⅱ.ゴム
弾力があり、柔らかい性質を持った高分子物質のことで、弾性ゴムともいいます。ゴムノキの樹液から作られる天然ゴムと、石油を原料として作られる合成ゴムがあります。天然ゴムが中南米からヨーロッパに伝わったのは15世紀以降で、それ以前から知られていたアラビアゴム(主に食品添加物として使われた)に似た感触だったため「ゴム」と名づけられました。
プラスチックの主な種類
プラスチックには大別して、汎用プラスチック、エンジニアリングプラスチック、スーパーエンジニアリングプラスチックがあります。
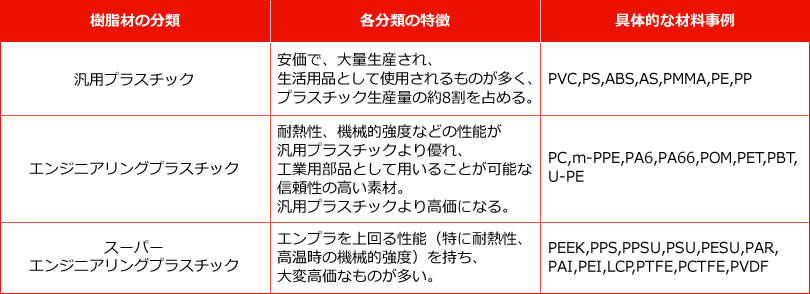
①.汎用プラスチックの主な種類
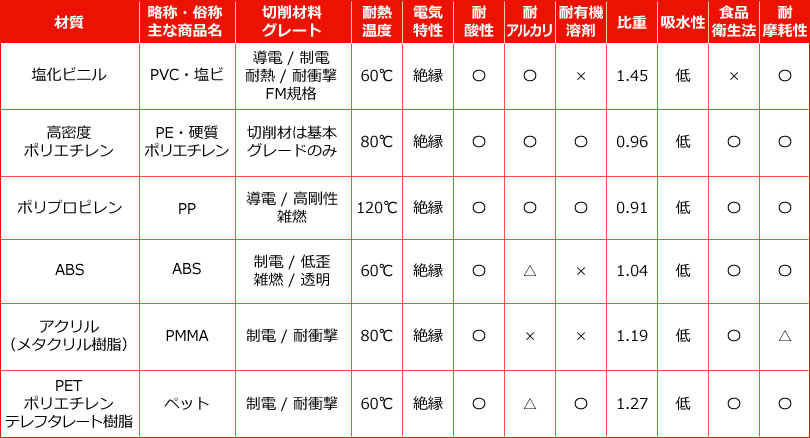
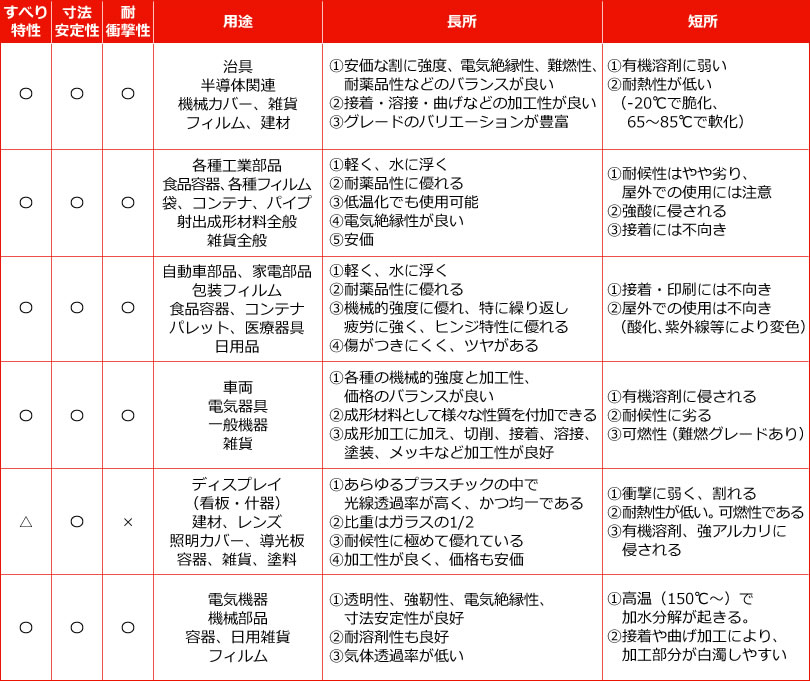
②.エンジニアリングプラスチックの主な種類
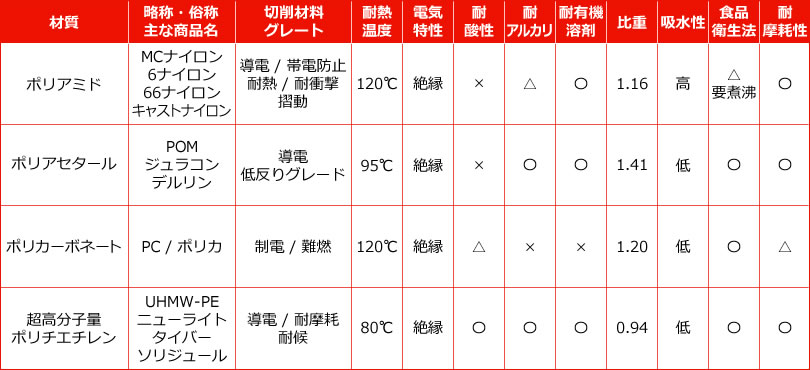
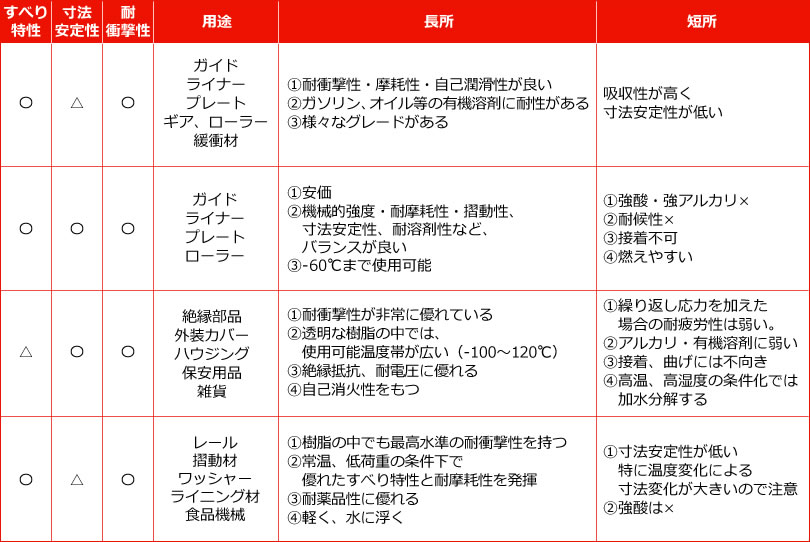
③.スーパーエンジニアリングプラスチックの主な種類
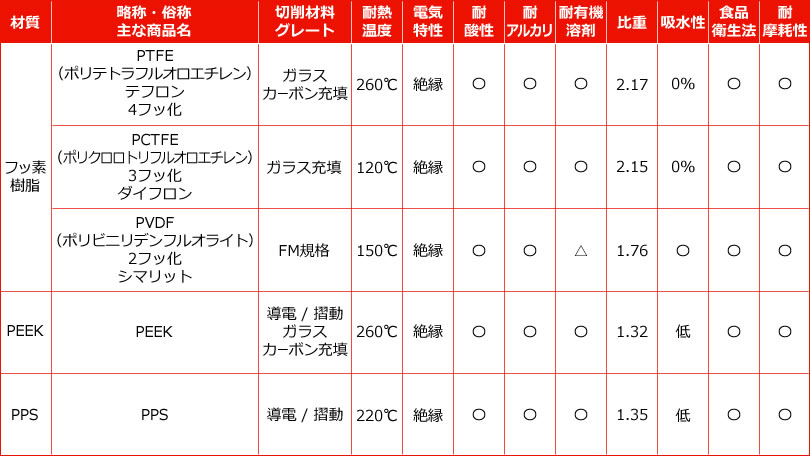
樹脂成形
樹脂成形は、熱可塑性樹脂と呼ばれる熱をかけると液状に変化する樹脂を用いて成形を行います。具体的な樹脂の成形方法としては、現在使用されている頻度などを考慮すると、大きく3つに分けることができます。その3つの方法とは、①.射出成形、②.ブロー成形、③.真空注型があります。以下では、各成形方法について紹介します。
①.射出成形
射出成形(Injection Molding)とは、加熱溶融させた材料を金型内に射出注入し、冷却・固化させることによって、成形品を得る方法です。複雑な形状の製品を大量に生産するのに適し、成形加工の一大分野をなしています。射出成形の工程は大きく分けて6つあり、Ⅰ.型締め、Ⅱ.射出、Ⅲ.保圧、Ⅳ.冷却、Ⅴ.型開き、Ⅵ.製品の取出しの順序で行われ、このサイクルの繰り返しで、製品を連続的に生産します。
②.ブロー成形
プラスチック成形品の内、中空の成形品を成形する最も代表的な方法が、ブロー成形(中空成形、吹込み成形)です。中空成形品としては、食品・飲料・洗剤・その他のボトル・タンク類が最も身近なものですが、その他にもエアダクト・燃料タンク・ウォッシャータンクなどのように中空部が必要な自動車部品があります。さらに、製品として特に中空部を必要としないが、中空をうまく利用した楽器ケース・工具ケース・コピー機のパネル、自動車のスポイラーなどの工業部品もブロー成形で成形されています。
具体的な成形法としては、ペレット状のプラスチック原料をブロー成形機にて溶かしてパイプ状にします(通称パリソンと呼びます)。この方法は、ホットパリソン法と呼ばれます。 パリソンは上から下に出てきますが、このパリソンを製品の外側のみ彫られている金型で挟み込み、中に空気を吹き込みます。このように空気で膨らませて製品を作ることをブロー成形といいます。
③.真空注型
真空注型は、金型の代わりに主にシリコン系樹脂の型を使用します。シリコン系樹脂の型を使用することで短納期・低コストで製品を製作することが可能となります。型に樹脂を流し込む際、真空状態で行うため、一般的なものよりも隅々まで樹脂をいきわたらせることができ、気泡などが生じにくいといったメリットがあります。
セラミックス・ファインセラミックス・マシナブルセラミックス
Ⅰ.セラミックスの主な種類
セラミックスは人為的な熱処理によって製造された所定の形状を持つ製品で、非金属材料として使用されています。セラミックスとガラスの関係性としては、セラミックスの中でも単一体でアモルファスと呼ばれる構造を持つ材料にガラスは属しています。
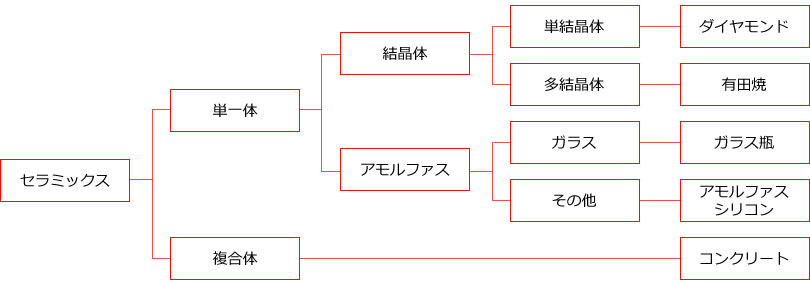
Ⅱ.ファインセラミックスとは
ファインセラミックスとは、セラミックスに、構造材料・電子材料・光学材料・生体材料・磁性材料を付加することで、材質特性に変化を与えているものを指します。
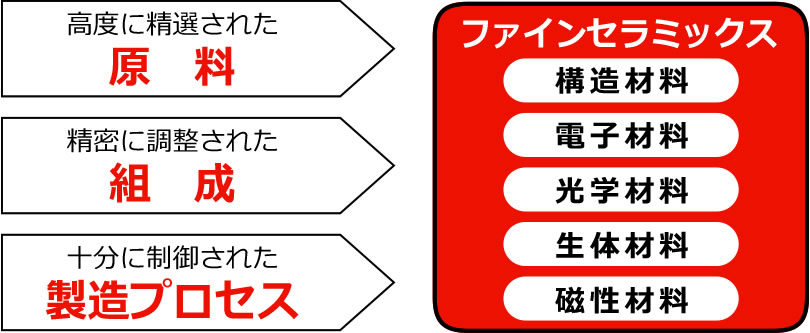
ファインセラミックスの概念図
Ⅲ.マシナブルセラミックスとは
マシナブルセラミックスは切削加工ができ、加工性がセラミックスと比較して大変良好で、微細・精密加工に適しています。少量の試作にも適しています。種々の特性を持った素材が素材メーカーより販売されており、お客様のご要望に合わせた素材を選定し購入して、加工を行います。
カーボン加工
カーボンとは元素の一種である炭素のことを表し、加工部品においては一般的にカーボンファイバーや炭素繊維プラスチック(CFRP)のことを表します。カーボンファイバーはアクリル繊維を焼く(炭化させる)ことで作られます。炭素繊維プラスチック(CFRP)は、カーボンファイバーに樹脂を染み込ませて成形し硬化させたものをいいます。
①.炭素繊維プラスチック(CFRP)の力学的特性
Ⅰ.引張特性
CFRPの引張比強度・弾性比率は、鉄やアルミ合金などに比べると3~9倍の強度を持ちます。ここでいう引張比強度とは、材料に引っ張り力が加わったときの材料の強さを表します。また、弾性比率とはその物質の変形のしにくさを表しています。
Ⅱ.耐疲労性
CFRPは、引張比強度・弾性比率に加えて、優れた耐疲労性をもちます。CFRPは、他の材料と比較して、繰り返し応力付与による破断応力が高く、繰り返し回数の増加に伴う破断応力の低下幅が小さいといった特性があります。
②.炭素繊維プラスチック(CFRP)の機能的特性
Ⅰ.熱・電気的特性
炭素繊維プラスチックは非常に熱膨張率に優れています。その特性から、300℃以上の温度差が生じる人工衛星のアンテナの寸法変化の防止や、非常に高い寸法安定性を必要とする電波望遠鏡のアンテナ等に活用されています。また、熱伝導率にも優れており、人工衛星における搭載機器からの発熱を効率的に宇宙空間へ排出するためのパネルなどに活用されています。
Ⅱ.化学的特性
- 耐熱性
炭素繊維強化プラスチックの耐熱性は、母材に主にエポキシ樹脂が用いられているため、基本的にはこのエポキシ樹脂の耐熱性で決まります。エポキシ樹脂の場合は120℃、硬化型エポキシ樹脂の場合は140~230℃程度となります。高い耐熱性が求められる航空機の構造材料用途として硬化型エポキシ樹脂が用いられています。 - 吸水率
吸水率に関しても、基本的にマトリックス樹脂の吸水率で決まります。 - 耐候性
長時間自然環境にさらした際の耐候性については、CFRP表面のエポキシ樹脂は太陽光や雨水などの影響により劣化しますが、下層の炭素繊維が露出すると光が炭素繊維によって遮断されるため、その後の樹脂の劣化は抑えられます。その結果、10年経過してもCFRPの引張強度はあまり変わりません。
③.炭素繊維プラスチック(CFRP)の機械加工
炭素繊維を加工する際には、加工温度、切削工具の摩耗、面粗度、切りくずといった問題に上手く対処する必要があります。
Ⅰ.加工温度
CFRPの熱伝導率が金属材料に比べて低いため、加工時に発生するほとんどの熱が切削工具に蓄積して100℃を上回る温度になり、その熱によるCFRPの劣化などにより加工性に影響を及ぼします。対策として、湿式加工、空気の流れ、液体窒素などによって冷却する必要があります。
Ⅱ.切削工具の摩耗
切削工具の摩耗の問題は、炭素繊維が硬くて難加工性であるため切削工具の刃先が摩耗することです。対策として、CFRPの機械加工に適した切削工具を使うことが望まれます。材質としては、ダイヤモンドが推奨されており、形状としては、Rドリルやボールエンドミルが推奨されています。
Ⅲ.面粗度
炭素繊維の配列方向と切削工具の当たる方向によって炭素繊維を引きはがす方向の負荷がかかるため面粗度が悪化しやすくなります。対策として、切削の方向と炭素繊維の配列の方向が平行となるのを避け、角度をつけるなどの工夫が行われています。
Ⅳ.切りくずの問題
CFRPの切りくずは比重が軽いので飛散しやすく、特に炭素繊維には電気伝導性があるため、電気装置への侵入を防ぐ必要があります。対策として、吸引装置の設置や切削液の付与などが行われています。