金属加工
機械加工
機械加工は、金属材料の表面を工具を用いて除去する操作のことをいいます。大きく分けると、機械加工には切削加工と研削加工があります。
①.主な切削加工方法
Ⅰ.旋盤加工
金属材料を回転させながら、バイトとよばれる切削工具を押し付け、表面を削り取る加工方法を旋盤加工といいます。材料が旋回することが特徴です。
Ⅱ.ボール盤加工
固定した金属材料にドリルとよばれる旋回溝を切った工具で穴をあける加工方法をボール盤加工といいます。ボール盤加工は、金属材料に穴をあける加工として多く使用されています。
Ⅲ.フライス盤加工
バイトを治具にセットし、治具を回転させながら固定した金属材料に押し付けて切削する方法をフライス盤加工といいます。平面の切削加工だけでなく、穴や溝を掘るような加工もフライス盤加工で加工することが可能です。
Ⅳ.エンドミル加工
エンドミルとよばれる切削工具を治具にセットし、治具を回転させながら固定した金属材料に押し付け、金属表面に溝や段差、穴などを掘る加工方法をエンドミル加工といいます。この方法では、金属材料を三次元的に移動させて複雑な形状を削り出すことも可能です。
Ⅴ.中ぐり加工
固定した治具にバイトを取り付け、円筒の内面を削る加工方法を中ぐり加工といいます。穴の経を大きくしたり、内面を手入れしたりするために、中ぐり加工が用いられます。
Ⅵ.歯切り加工
円盤状の金属材料の外周を削り出し、歯車を作出する加工方法を歯切り加工といいます。ラックもしくは、ホブという切削用の工具を用いて、円盤の外周に押し付けて歯車を削り出します。
Ⅶ.ブローチ加工
ブローチとよばれる特殊工具を用いて、スプライン穴などの様々な形状をした穴の内面加工を行います。ブローチ加工は、ブローチを引き抜くだけで、粗加工から仕上げ加工まで一工程で加工ができます。
②.主な研削加工方法
Ⅰ.円筒研削
円筒形の金属材料の表面を研削するために、円筒を回転させ、回転させた砥石を押し付けながら移動させることで、表面を削り取ります。これを円筒研削といいます。
Ⅱ.内面研削
円筒の内面を砥石で削る加工方法を内面研削といいます。内面の仕上げ加工には欠かせない加工法です。
Ⅲ.平面研削
平板の表面を削る方法を平面研削といいます。砥石もしくは平板を移動させながら表面を削ります。
③.旋盤加工
金属材料を回転させながら切削し、バイトとよばれる切削工具を押し付けて切削する加工方法を旋盤加工といいます。円筒状の材料の外周を成形します。
Ⅰ.旋盤加工の種類
旋盤加工には大きく分けて5つの加工パターンがあります。1つ目は、バイトを円筒の外周に押し付けて削り、円筒の外形を小さくする外径切削加工です。バイトもしくは金属材料を移動させることで、広範囲な円筒表面を切削します。2つ目は、回転している金属材料の内径を削っていく内径切削加工です。3つ目は、円筒に溝を掘る突切り加工です。バイトの位置を固定しておくことで円筒の一部分の外周だけを切削し小さくすることが可能になります。4つ目は、外周削りのバリエーションであるねじ切り加工です。バイトもしくは金属材料の移動と切削を組み合わせて円筒の外周にねじ切りを行います。5つ目は、回転している金属材料の正面に穴あけ工具を当てて行う穴あけ加工です。内径切削加工の前工程として行います。
④.ボール盤加工
ドリルで金属材料に穴をあける加工をボーリングといいます。ボーリング用の機器がボール盤です。
Ⅰ.ボール盤加工の種類
ボール盤加工に用いる工具はツイストドリルとよばれます。ねじれた溝を持ち、個の溝を通して切削油を供給したり切削屑を排出したりします。主な加工方法は、ドリルによる単純な穴あけ加工、開いている穴の径を広げるために穴経よりも太いドリルを使用する穴広げ加工、リーマ―という工具を用いたリーマ―加工、タップをねじ込むタップ立て加工などがあります。それ以外にも、中ぐり加工や座ぐり加工など、すでにあいている穴の形状を整える加工もあります。
Ⅱ.ボール盤の種類
ボール盤は、ドリルを取り付けて回転させるスピンドルを保持して上下に移動させる機能と、加工する金属材料を固定する機能を持っています。直立ボール盤は、この基本機能だけのもので、ドリルは上下するだけで、金属材料は固定、もしくは回転盤にのせられて回転するだけの機能しかありません。ラジアルボール盤は、ベッド上に直立する柱(コラム)に旋回・上下できるアームがあり、主軸頭が移動する構造になっています。精巧に穴をあける加工に利用します。
Ⅲ.ボール盤加工の手順
ドリルでの穴あけ加工は、一度の加工で行うと、寸法精度も穴の内面粗さもばらついてしまいます。ドリルでの穴あけ加工は、通常3つの工程で行われます。第一に、目的寸法よりもわずかに小さな径の穴あけ加工を行います。次に、穴広げ加工で目的寸法の穴径に加工します。さらに、穴の内面を、仕上げ加工用の工具で滑らかにします。
⑤.フライス盤加工
フライス盤加工は、金属材料を固定し工具を動かして切削する金属加工方法です。フライス盤加工は、現場用語では「ミーリング」といわれることもあります。
Ⅰ.フライス盤加工の種類
フライス盤加工では、フライス工具とそれを支える治具の組み合わせと、金属材料に対する切削回転方向を変えることにより、平面加工だけでなく、段差を掘ったり溝を削ったりすることも可能です。もっともよく使われるのが正面フライス加工です。
⑥.エンドミル加工
エンドミル加工は、底刃と外周刃を持つエンドミルとよばれる工具で、金属材料を切削する方法です。
Ⅰ.エンドミル加工の種類
エンドミル加工は、フライス盤加工やボール盤加工とほぼ共通します。金属材料に段差をつける段削り、側面を削る端面削り、ボール加工のように穴をあける穴あけ加工もあります。エンドミルは、底刃が平らなものをエンドミル、もしくはスクエアエンドミル、ボール状に丸くなったものをボールエンドミルといいます。
⑦.中ぐり加工・歯切り加工
中ぐり加工と歯切り加工は、機械加工の中でも特殊な加工です。円筒形の金属材料の内面切削をするのが中ぐり加工で、歯車の歯を作出するのが歯切り加工です。
Ⅰ.中ぐり盤の種類
中ぐり盤には、中ぐりをする工具を取り付けるスピンドルという主軸が横方向にある横中ぐり盤と、縦方向にある立中ぐり盤があります。中ぐり加工は、切削工具を取り付けた主軸を片持ちで支えながら回転させる方法とラインバーを通して支点を作り、両側で支える方法があります。切削工具がスピンドルの先端で金属材料と接するので、たわみやブレなどが生じて加工精度に影響するのを防ぐために、中ぐり盤は頑丈で大きなスピンドルを備えています。
Ⅱ.歯切り盤の種類
この工作機械によって作出された歯車が使用されることが多く、一般の歯切り盤は創成法で歯車を作出しますが、作出すべき歯形をもった総形フライスを用いてフライス盤によって加工する場合もあります。
Ⅲ.ブローチ盤の種類
ブローチを縦方向に取り付けるものを立てブローチ盤、横方向に取り付けるものを横ブローチ盤とよびます。
⑧.研削加工
研削加工は、砥石を用いた金属材料の表面加工方法です。大きく分けて、円筒研削と平板研削があります。砥石での研削は、様々な欠陥を生み出します。欠陥を防ぐために、砥石の性質を理解し、適切な研削条件で使用する必要があります。
Ⅰ.円筒研削の種類
両端のセンターで支持し回転させた円筒形の金属材料の表面を回転させた砥石で研削するのが円筒研削です。円筒研削には主に3つの方法があります。1つ目は、砥石を金属材料の軸方向に平行移動させながら研削を行うトラバース研削、2つ目は、砥石あるいは金属材料を砥石半径方向へ移動させながら行うプランジ研削、3つ目は、金属材料の回転軸に対して一定の角度を設定し、コマ型の砥石を押しあてて加工するアンギュラ研削です。
Ⅱ.平面研削盤の種類
平面研削は、金属材料を保持したテーブルを動かして平面を加工します。金属材料の運動方法により、横軸往復テーブル型、横軸回転テーブル型、立軸往復テーブル型、立軸回転テーブル型に大別されます。
Ⅲ.研削で発生する欠陥
研削する際に金属材料に発生する可能性がある欠陥は、表面欠陥を始めとして数多くあります。砥石は研削を続けていると、砥石の研削面がつぶれてくるため次第に研削が難しくなります。研削音が軋んでくるので、観察していれば判断できます。この状態のまま研削を続けると、金属材料の表面のところどころに研削焼けとよばれる光沢のある部分が発生します。このような状態になった砥石は再研磨を行って研削面を復活させて使用する必要があります。他にも発生する可能性がある欠陥には、研削熱で発生する研削割れがあります。また、砥石の周期的な動きが転写したビビリマークや、研削がうまくいかず表面に入る引っかき傷、円筒のどの方向でも均質に削る事が難しくなりひしゃげた円筒になる真円度不良が発生するケースもあります。
Ⅳ.砥石の特長
砥石を選択する際には、砥石の形や使用方法、砥石の材質を考えて選択する必要があります。これらの選択を誤れば、金属材料の研削品に品質異常が発生したり、操業や設備のトラブルにつながる恐れがあります。研削加工方法に適した形状の砥石を選択するほかに重要なことは、被研削材がどのような材質のものなのか、また最高使用周速度をどれくらいにするのかを明確にすることです。また、砥石の材質は、砥粒の種類でかなりの部分が決まります。アルミナ系かダイヤモンド系かの選択で、砥石の性質の大部分が決まってしまいます。粗い粒度の砥粒は粗研削用に、細かい粒度の砥粒は仕上げ研削用に使用します。
リバースエンジニアリング(設備保全部品加工)について
リバースエンジニアリング(設備保全部品加工)は、通常の部品加工とは少し異なります。普通の加工は、図面ありきで製作・加工をします。しかし、リバースエンジニアリング(設備保全部品加工)は、そういった通常の流れとは逆に、まず図面を作成します。つまり、図面がない部品でも製作・加工が可能となり、すでに生産中止になっている部品でも製作・加工することが可能なのです。
絶対に止めることができないラインにおける設備保全部品を緊急で製作できるのが、リバースエンジニアリング(設備保全部品加工)のメリットです。
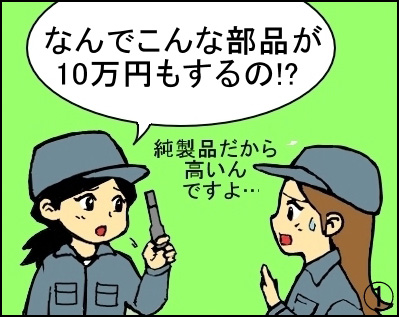
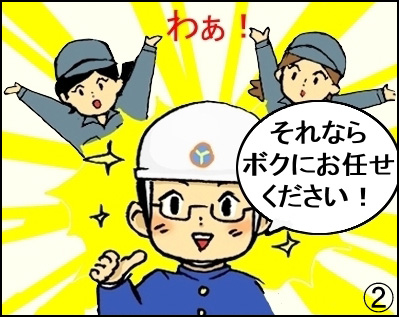
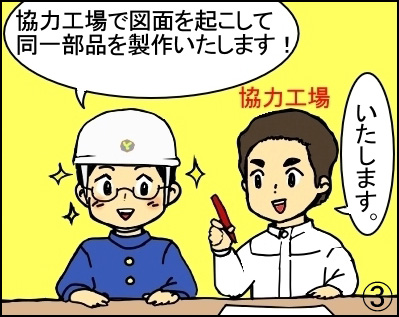
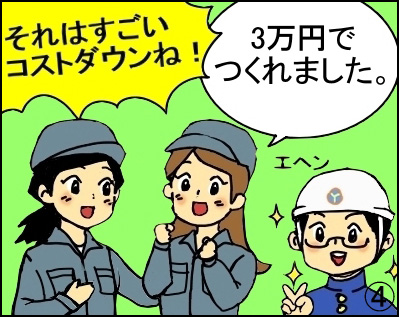
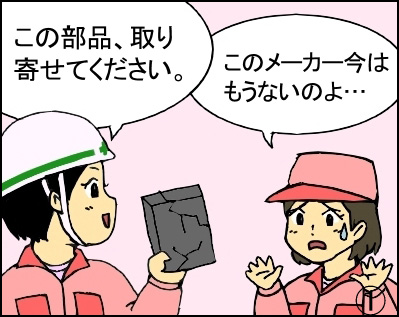
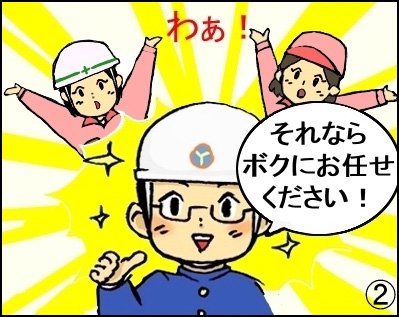
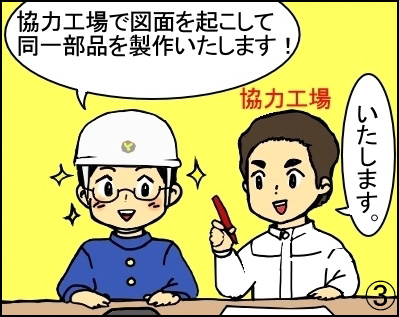
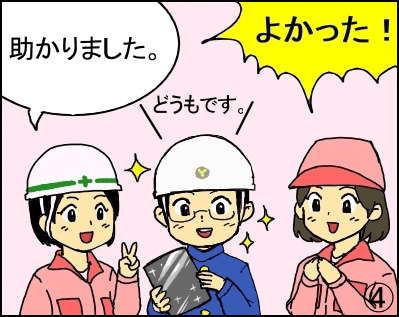
リバースエンジニアリング(設備保全部品加工)によるメリット
Ⅰ.生産中止部品のリバースエンジニアリング(設備保全部品加工)
使用している機械が生産中止になっており、機械の構成部品がすでに製作されていないといったケースがあります。このような場合でも、リバースエンジニアリング(設備保全部品加工)によって、機械の構成部品を製作することが可能です。使用している機械の急な故障に対する緊急対応が、リバースエンジニアリング(設備保全部品加工)によって可能となるのです。
Ⅱ.消耗部品のイニシャルコスト低減によるコストダウン
一般的に、メーカー純正品は高価です。当然ながら、メーカー純正品でなければならないような設備全体の信頼に関わるパーツであれば、たとえ高価であっても純正品を使用する方がベターといえます。しかしながら、こういったケース以外の場合は、リバースエンジニアリング(設備保全部品加工)によって、消耗部品のスペアパーツを適正価格で製作すれば、コストダウンを実現することができます。
Ⅲ.耐久性の向上によるコストダウン
リバースエンジニアリング(設備保全部品加工)によって、現行の部品に特性付加加工(表面処理加工など)を行ったり、さらに耐久性のある材質に変更することで、ランニングコストをコストダウンできる場合があります。